Es war schnell erledigt: In wenigen Tagen waren die Hallen beim Dämmstoffhersteller Isover in Speyer ausgeräumt, die alten Anlagen abgebaut und die neue Technik installiert. Die Arbeit und die Investitionen in Höhe von circa 10 Mio. Euro, die in die Maßnahmen zur Herstellung der neuen Wolle Lanaé geflossen sind, waren dafür umso größer – und umso größer auch die Freude, dass man nun für die ganze Mühe mit der Leserauszeichnung zum Produkt des Jahres 2024/2025 belohnt wurde, die der Dähne Verlag über sein diy-Fachmagazin auslobt.
Neu an der Mineralwolle ist weniger der hohe Anteil an verarbeitetem Altglas von 80 Prozent, denn darin hat der Hersteller bereits lange Erfahrung – nicht ohne Grund setzt sich die Bezeichnung der Marke Isover aus den französischen Worten Isolation (Dämmung) und Verre (Glas) zusammen –; es ist vielmehr das neue und auf natürlichen Stoffen basierende Bindemittel, das die Mineralwolle zusammenhält. Dieses wird in einem patentierten Verfahren hergestellt und zugeliefert und basiert auf Stoffen aus der Zucker- und Getreideherstellung.
Eine weitere Besonderheit ist die dichte Verpackung, die durch ihre komprimierte Form sowohl für einfache Lagerung und Transport als auch für eine geringere Feuchtigkeitsbildung bei der Aufbewahrung im Freien sorgt. Darüber hinaus ist die Verpackung für einfacheres Recycling nur minimal bedruckt und besteht zu 30 Prozent aus Rezyklat. „Wir hätten gern einen höheren Anteil verarbeitet“, erklärt DIY-Vertriebsleiter Heiko van Eck, „doch durch den großen Druck, der auf die Verpackung wirkt, ist das bislang nicht möglich.“
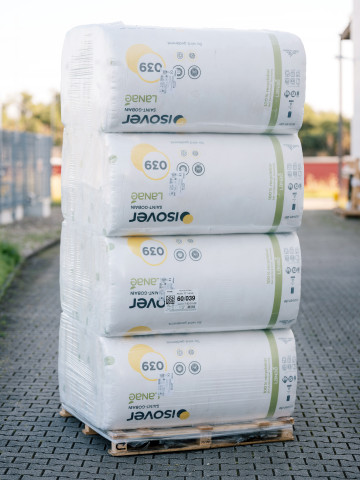
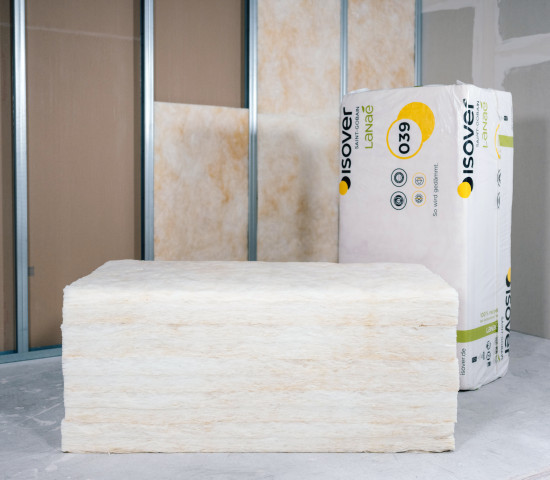
Nach und nach wurden und werden etliche Glaswolle-Produkte auf Lanaé umgestellt – die Trennwandplatte, mit der Isover bei der diy-Auszeichnug überzeugte, bereits im September 2024, die Klemmfilze 034 im Februar und die Klemmfilze 031 folgen jetzt in diesem Mai. Lanaé setzt sich übrigens aus dem lateinischen Wort für Wolle, Lana, und é zusammen, was für écologique steht.
Die Rückmeldungen, die er dazu bislang erhalten habe, seien alle positiv, berichtet van Eck. Die Anwender sind begeistert vom geringen Gewicht und der weichen Struktur. „Da juckt und kratzt nichts mehr“ – ist ein häufiger Satz von Kunden, die schon länger mit Glaswolle arbeiten. Ebenso überzeugt die einfache Verarbeitung: Das Material lässt sich leicht schneiden und die Klemmfilze lassen sich, wie der Name schon sagt, einfach und sicher zwischen die Sparren klemmen – was die Produkte ideal auch für Heimwerker macht, die bisher wenig Erfahrung im Einbau von Dämmmaterial haben.
Sollte es doch einmal haken, bietet Isover mit seinen mehr als 600 Erklärvideos auf Youtube Informationen zu seinen Produkten und der jeweiligen Verarbeitung. Man habe mit über 20. Mio. Aufrufen die höchste Klickrate der Branche in Europa, verkündet der Vertriebsexperte stolz. Besonders hoch sei die Klickrate bei den Vario-Produkten zur adaptiven Dampfbremsfolie, einem erklärungsintensiveren Produkt aus dem Hause Isover.
Auch für den Handel ist gesorgt – mit individuellen Konzepten und Material für den POS wie Regalstoppern, Kopfblenden und Broschüren. „Wir brauchen hier mehr Omnichannel“, ergänzt der Fachmann und kündigt Maßnahmen an, um den Onlineauftritt von Isover stärker mit den stationären Märkten zu verknüpfen. Ebenso praktisch: Durch die gute Zusammenarbeit mit dem Unternehmen Rigips, das wie Isover ebenfalls unter dem Dach der französischen Unternehmensgruppe Saint-Gobain steht, ist es auch möglich, ein System aus Profilen, Dämmstoffen und Gipskartonplatten anzubieten – also eine gesamte Trennwand aus einer Hand.
Neben der vereinfachten Lagerung und klareren Kommunikation durch die neue Verpackung bietet der Hersteller dem Handel und seinen Kunden auch verschiedene Rücknahme-Services. Das gilt zum einen für die Rücknahme von Paletten, die mit einem entsprechenden Symbol gekennzeichnet sind, und zum anderen für wieder ausgebaute Glaswolle, die dem Produktionsprozess wieder zugeführt werden kann. Dafür hat Isover zusammen mit Rigips die Initiative Easy Eco ins Leben gerufen: Der Verarbeiter kann Big Bags kaufen, in denen gebrauchte Dämmmaterialien gesammelt werden, der Dienstleister holt sie ab, bereitet sie wieder auf und liefert sie zurück nach Speyer. Der Anteil sei bislang noch klein, merkt van Eck an, das liege aber auch in der Natur der Sache. „Die Wärmeschutzverordnung hat erst vor 40 Jahren begonnen, davor waren viele Häuser gar nicht gedämmt. Bis die neuen Häuser abgerissen oder modernisiert werden, dauert es noch eine Weile.“
Der Vertriebsleiter [Heiko van Eck] ist überzeugt, dass Isover mit Lanaé einen Nerv trifft. Denn ein gut gedämmtes Gebäude reduziere den Energiebedarf für die Heizung oder Kühlung der Räume – das senke den CO2-Ausstoß, sei vor dem Hintergrund zunehmend heißer Sommer besonders zeitgemäß und schone, insbesondere mit Blick auf die Heizkosten, den Geldbeutel.
Neue Impulse sind dringend nötig, denn es liegen schwierige Monate hinter der Branche. „Der Bedarf ist stark zurückgegangen, der Markt ist deutlich rückläufig“, berichtet van Eck. Der Grund dafür: Es seien deutlich weniger Wohneinheiten fertiggestellt worden. Hoffnung setzt er in die neue Regierung. „Es wird aber Zeit brauchen“, fügt er an und fordert von der neuen Koalition mehr Anreize zum Bauen und ein stärkeres Engagement in Richtung Sanierung und Renovierung. „Der Tiefpunkt ist erreicht. Nun rechnen wir mit leichten Zuwächsen für das laufende Jahr“, hält er fest.
Diese Zuversicht zeigt sich auch darin, dass Isover laufend in das Werk Speyer investiert. Nach der Einführung einer neuen Schmelztechnologie vor fünf Jahren und den Anpassungen für die Umstellung auf Lanaé steht in den kommenden drei Jahren die Elektrifizierung des Heißbereichs an: Die Schmelzwanne soll nicht mehr mit Gas, sondern mit grünem Strom befeuert werden, der unter anderem von drei Fußballfeldern großen PV-Modulen auf dem Dach kommt. „In den anderen Fertigungsbereichen setzen wir schon lange nur Grünstrom ein“, ergänzt Werksleiter Nikolaus Wesely. Er sieht Isover mit Blick auf das Thema Nachhaltigkeit gut aufgestellt. „Bereits jetzt haben wir in Summe eine tolle Ökobilanz. Der hohe Energieaufwand zum Einschmelzen des Altglases wird durch die Einsparungen wieder ausgeglichen, die das Produkt in der Anwendung beim Endkunden bringt“, führt er aus.
Bei einem Rundgang über das Gelände erklärt [Werksleiter Nikolaus] Wesely die Produktionsabläufe und Feinheiten der Herstellung von Glaswolle – dabei kommt ein Thema immer wieder auf, was dem Fachmann besonders am Herzen liegt: Arbeitssicherheit. „Wir haben eine geringe Unfallquote“, unterstreicht er, „weil wir auch auf die Kleinigkeiten achten.“ Dazu gehört, dass jeder Mitarbeiter und Besucher vor dem Betreten des Werks eine Sicherheitsunterweisung absolviert, dass die Schutzbrille auf der Nase, der Gehörschutz auf den Ohren, und der Helm auf dem Kopf sitzt, dass Handläufe genutzt, die Sicherheitsweste getragen werden und keiner vom markierten Weg abkommt.
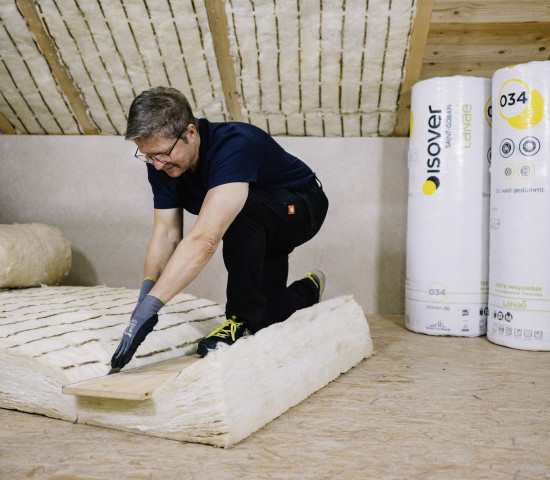
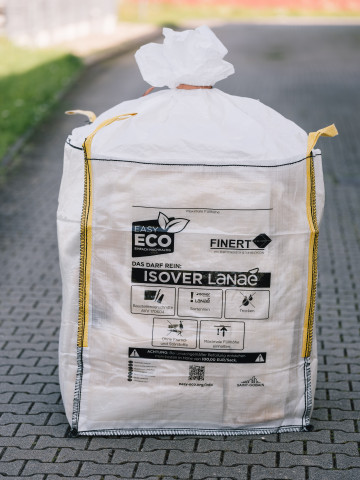
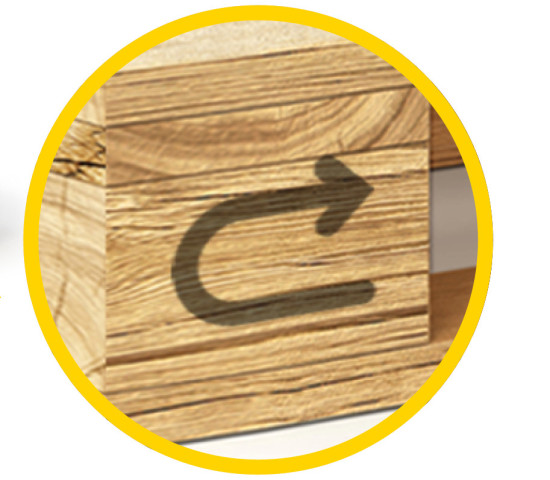
Der Grund für seine Vorsicht wird schnell klar: Hier werden tonnenschwere Materialien befördert, riesige Lkw laden Paletten auf, das Flüssigglas ist heiß wie Lava und Maschinen zerkleinern in Sekundenschnelle die Dämmstoffe und Vorprodukte – und das alles automatisiert. „Alles beginnt am Scherbenlager“, startet Wesely. Hier kommen täglich zehn bis 15 Lkw-Ladungen mit je 25 Tonnen Flach- und Hohlglas an. In einem speziellen Sieb werden Keramik- und Kunststoffbestandteile herausgefiltert, denn „die machen unsere Anlagen kaputt“, so der Werksleiter. Die Scherben werden mit Kalk, Sand und Soda versetzt, in Silos befördert und von dort aus wird das Gemenge in die Schmelzwanne gefüllt.
Die nach der Tochter des Anlagenleiters Leah benannte Wanne ist 110 m2 groß und fasst rund 300 Tonnen Flüssigglas. Sie läuft rund um die Uhr, an sieben Tagen in der Woche. Sauerstoffgasbrenner erhitzen das Gewölbe auf 1.400 Grad, das wiederum über Strahlungswärme das Glas schmilzt. Die Masse wird im Anschluss vorbei an den Dosieranlagen für das Bindemittel weiter zur Zerfaserung transportiert. Hier zeigt sich, warum jegliche Fremdstoffe für Probleme sorgen: Die sogenannten Schleuderringe sind mit winzigen Löchern versehen, durch die das Flüssigglas mit 2.000 Umdrehungen pro Minute geschleudert und die Wolle auf ein Fließband abgelegt wird, wo sie sofort erkaltet. Isover macht sich dabei Zentrifugalkräfte zunutze. Den so entstandenen Fasern werden kleine Mengen von Bindemittel zugeführt. Die Idee für diesen Schleuder- und Ziehprozess hatte der Erfinder des Verfahrens 1931 bei einem Kirmesbesuch, wo er von der Herstellung der Zuckerwatte inspiriert wurde.
Das Rohmaterial wird vom Fließband in einen Trockenofen transportiert. Gasbrenner blasen heiße Luft in den Ofen und härten so das Bindemittel aus. Mithilfe eines Wasserstrahls und einer Schlagschere wird die Mineralwolle auf die benötigten Maße geschnitten. Jeglicher Verschnitt wird wieder dem Produktionsprozess zugeführt. Dadurch, dass man das verwendete Wasser so weit wie möglich im Kreislauf führe, unterstreicht Wesely, erreiche man einen sehr geringen Wasserverbrauch von 60 bis 100 Kubikmeter pro Tag.
Der Weg zur Verpackungsanlage führt vorbei an einer Infotafel, wie man sie aus dem Lean Management kennt, ein Ansatz der zur Steigerung der Effizienz beiträgt, etwa durch bessere Organisation, vorausschauende Planung, Vermeidung von Arbeitsunfällen und eine bewusste Fehlerkultur. „Produktivität ist bei uns klar ein Thema“, bestätigt der Werksleiter, „ebenso Automatisierung.“ Man gehe derzeit von Industrie 2.0 in Richtung Industrie 4.0, wo deutlich präventiver gearbeitet werde.
Wesely ist, ebenso wie sein Kollege aus dem Vertrieb, schon lange bei Isover beschäftigt. Man merkt ihm die Begeisterung für seine Tätigkeit an. „Die Arbeit ist super vielseitig“, schwärmt er. Das Unternehmen ermuntere seine Mitarbeitenden dazu, verschiedene Bereiche kennenzulernen. So hatte Wesely etwa die Gelegenheit, ein Werk in Großbritannien mit aufzubauen.
Auch in der Verpackung läuft alles automatisiert ab: Eine spezielle Maschine stapelt die Pakete auf eine Palette – 18 Rollen passen jeweils darauf – anschließend vermisst die Anlage die Palette [sie] und stülpt eine Folie darüber. Um die Ware zusätzlich zu komprimieren, wird bei manchen Produkten Hitze und eine Schrumpffolienverpackung eingesetzt.
Anschließend können die Paletten verladen werden. Das geringe Gewicht der Lanaé-Produkte komme vor allem dem Anwender beim Handling der Platten zugute, sagt Wesely. „Herausfordernd für uns ist eher das Volumen der Dämmplatten.“ Daher wird der verfügbare Lagerplatz in Speyer an manchen Tagen knapp. Außerdem erschwere das hohe Volumen den Transport – Isover nutzt daher Jumbo-Lkw, in die 24 Paletten hineinpassen. Doch selbst damit werde der Ladevorgang oftmals zur Millimeterarbeit, merkt der Werksleiter an.
Von Speyer aus gehen die Waren in das gesamte Bundesgebiet, gelegentlich auch ins Ausland – und übrigens, Schwestergesellschaften von Isover G+H sind in fast 60 Ländern präsent. Was überall gleich bleibt, ist der Anspruch des Herstellers: mit nachhaltigen Dämmstoffen Systemlösungen für gesündere und komfortablere Gebäude zu entwickeln – entsprechend dem Saint-Gobain Unternehmens-Purpose „Making the World a better Home“.
Dämmstoffe aus Deutschland – mit französischer Unterstützung
Isover produziert an vier Standorten in Deutschland Mineralwolle. In Speyer und Bergisch Gladbach wird Glaswolle gefertigt, in Ladenburg liegt der Fokus auf Steinwolle, die sich durch einen deutlich höheren Brandschutz, etwa für Fassaden und Flachdächer auszeichnet und im norddeutschen Lübz entsteht Ultimate, eine Dämmlösung, die der Steinwolle ähnlich, doch deutlich kompakter und leichter ist. Glaswolle wurde 1931 in dem Werk in Bergisch Gladbach erfunden. Der französische Glas-Spezialist Saint Gobain, dessen Vorgänger-Manufaktur bereits den Spiegelsaal im Schloss Versailles ausgestattet hatte, erkannte das Potenzial, das in dem neuen Dämmstoff steckte, und übernahm das Gladbacher Unternehmen 1936, das 1971 wiederum mit dem Ludwigshafener Dämmstoffspezialisten Grünzweig + Hartmann fusionierte.
Dies ist die Langversion des Beitrags aus der Printausgabe diy 5/2025